The beginning of each year is a good time to reflect on the time that has passed and anticipate what the year ahead will bring. As The Hagerman Group embarks on 110 years in business, we have a rich history to appreciate and reflect on, yet we also keep a constant eye to the future, seeking innovations that will bring benefits to our clients, their projects, and the industry.
This month’s blog features two perspectives—one from Terry Greene, executive vice president, who has worked in the construction industry since 1975, and another from Joel Fleming, a project manager who has been in the field for the past five years. Despite their difference in years, both Joel and Terry have a few things in common. They’re both working on the Franklin College Science Center—Joel as project manager and Terry as project executive. They’re both future-thinking. And, they both have thoughtful viewpoints about how the construction industry is evolving.
A lot of aspects of construction have stayed the same—we still use steel, concrete, masonry and paint. In addition, relationships and communication have always been important. But a lot has changed, and the pace of that change is seemingly accelerating as we look toward the future.
Looking back: A dramatically different landscape
While looking back often goes hand-in-hand with nostalgia, many areas of construction have changed for the better, from technology to culture. “I started working in construction more than 40 years ago, and the changes in the industry have been phenomenal,” said Terry. Technology has advanced exponentially, from how we communicate with each other to how much computing power we have available.
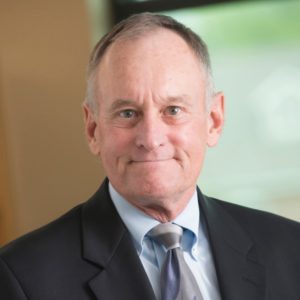
In the ‘70s, the administration of projects went slowly. “You could only get a drawing as fast as it was shipped or delivered by a courier, and that was after you had a printer make blueprints,” Terry said. “Email and mobile phones didn’t exist. We used a ‘telecopier,’ the precursor to the fax machine. If someone had to get ahold of you, they would page you and you had to find a landline to call them back.”
Terry also remembers when—in college—he upgraded from a slide rule to a five-function Texas Instruments calculator. “It was a TI-10 calculator and I paid $120 for it,” he said. He also recalls using punch data cards and a mainframe computer to put out the schedule for his first project. “You made one error, and everything crashed.” His first computer—purchased in the ‘80s at Radio Shack—had a memory capacity of just 16K and cost $2,000. “The computer power we have now is incredible,” Terry said.
The culture of construction has also improved significantly over the years. Terry recalled early in his career when there was a lack of regulation, diversity, and emotional intelligence in the industry. Jobs were often done on a handshake rather than a contract, which resulted in a lot more change orders. Long hours were the norm, and “whoever had the strongest personality rose to be a leader—not necessarily the smartest person,” Terry said.
Looking forward: A continual evolution
Fortunately, a lot of advancements have been made over the past 40 years, and more are on the way, from how people communicate to how they work.
Communication and technology
Communication has evolved drastically, and continues to do so at a rapid pace. Advances in technology are helping construction companies keep owners better informed, in real time. As a result, owners can get a richer understanding of their buildings, both during and after construction.
“We can show owners a lot of information in a way that is easy to comprehend,” said Joel. “With Procore, our construction management software, we can go into more detail and easily share photos and drawings through the cloud.”
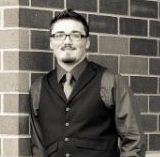
In addition, with tools like augmented reality and virtual reality, Hagerman can walk owners through their future buildings, helping them get a sense of the space and facilitating better informed decisions that can reduce costs. Through webcams and drones, owners can view the progress of their facilities over time.
“These communication tools help us build an open, honest relationship with owners by increasing transparency, and there’s more collaboration between the owner, architect and contractor,” Joel said. “We’ve also increased efficiency in the field because we can address issues quickly.”
Thanks to photos captured during the construction process combined with imaging software, owners can now view 3D images of what’s behind walls, rather than having to review drawings of what was built. This provides a helpful resource for systems maintenance and future renovations.
“The development of ever-changing, sophisticated software and applications have helped improve our efficiency,” said Terry. “Every couple of months, there’s something new and better.”
Delivery models and construction methods
In addition to communication methods, working methods are changing, too. When it comes to how projects are delivered, there are more options available than ever, from traditional design-bid-build to construction manager at risk.
Prefabricated and modular construction is on the rise, with an increase in the amount of building components manufactured in a controlled environment before arriving at the project site, where they can quickly be installed.
“For a parking garage project in Bloomington, we used architecturally precast concrete for the facade, which saved money and cut time from the project,” Joel said. “Logistically, since it came in on panels, it was easier to stage the materials on the tight site.”
Materials selection and sustainability
The way we use materials is also evolving. “Looking ahead, we’re going to start seeing new materials in construction,” Terry said. “Just like we’ve seen aircrafts move from steel and aluminum to carbon fiber, we’ll start to see new materials in construction. And as wireless systems continue to take over, some materials will go away completely.”
Materials selection is just one part of an overall concept that continues to advance and evolve—green building and sustainability. “The industry has come a long way, even in the past 10 years,” said Joel. “There’s a lot more interest in sustainability and building green. Even when projects aren’t pursuing LEED certification, we can still think eco-friendly by selecting regional materials, adhering to a recycling and waste plan, and incorporating lean construction practices in the field.”
“Mechanical systems have changed significantly in recent years, with buildings becoming more and more energy efficient,” said Terry.
While no one can predict the future with certainty, looking at the past and current trends and thinking about the future can help us understand where we came from, appreciate how far we’ve come, and better prepare for what’s next. Here’s wishing you the best in 2018, and beyond.